Controlled environment agriculture (CEA) describes approaches to growing crops under managed environments in order to optimize resources and productivity. Many different crops can be grown in CEA systems, which control the aerial and root environment to keep plants in their comfort zones. One CEA approach is an indoor hydroponic system, which can be used to grow fruits and vegetables.
While the term CEA commonly describes indoor or covered plant production, CEA includes different levels of technology integration achieving an optimum plant growth environment. These include:
- Low-level integration and environmental control in open field crop production, like the use of shading and irrigation systems.
- Passive environmental controls for growing crops in soil, such as covering materials and structural design in high tunnels.
- Integrated sensors and active control systems in greenhouse production systems to control the environment and supplement sunlight.
- Full indoor production, the most complex production system, which uses technology to create an optimum environment for plants without relying on the external environment.
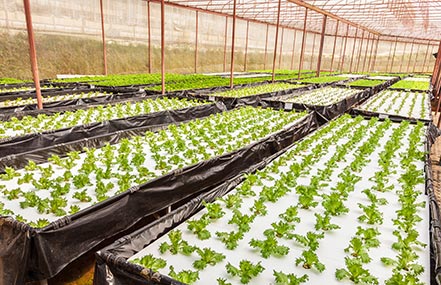
Indoor hydroponic systems provide support, water, and nutrients to crops. Plants in hydroponic systems may either be grown with the roots in direct contact with liquid nutrient solutions supported by floating rafts or plastic trays, or with roots grown in containers with other types of soilless media (coconut coir, rockwool, peat mixes, etc.). In soilless production systems, irrigation water delivers all the plant’s nutrient needs.
Advantages and disadvantages
Hydroponic systems offer benefits for food production (Table 1). Hydroponic crops can be grown year-round. Crop production may continue during winter, and covered CEA systems protect crops from weather-related damage. Hydroponic systems can produce higher yields per square foot than field production.
Table 1. Benefits and challenges of hydroponic systems.
Benefits | Challenges |
---|---|
No seasonality | High investment |
Food safety | High energy use |
Food access and urban agriculture | Limited crops |
High yields | Higher production costs |
Resource efficiency (except energy) | Requires specialized skills |
Other benefits of hydroponics are related to the ability to control and mitigate production risks. For example, crops grown indoors are less likely to come into contact with common foodborne pathogens from wildlife vectors. Hydroponic crops can also be grown where arable land is less available. This versatility makes hydroponic systems appealing for urban agriculture.
Like any production system, there are trade-offs for hydroponic systems. Hydroponic systems require substantial capital investment and can have higher production costs (especially energy) than open field crop production. Only crops with high yield potential and/or higher selling prices may be economically viable in a hydroponic system, which may result in farms with less crop diversity and fewer revenue streams. Hydroponic crops also require a different producer skill set than field-grown crops.
What can you grow in hydroponic farming systems?
Leafy greens and tomatoes are among the most popular crops grown hydroponically. Strawberries, cucumbers, microgreens and some herbs are other possibilities for hydroponic production.
Types of hydroponic systems
Hydroponic systems can be categorized into water-based and growing media-based systems, each supports the roots differently. Water-based systems use floating rafts, plastic trays or plastic net pots to support the plant and expose the roots directly to nutrient solutions. In media-based systems, the roots are supported in soilless growing media held in containers, Dutch buckets, grow slabs or plastic bags.
Hydroponic systems can also be “closed” or “open.” In closed systems, the nutrient solution recirculates in the system and is constantly reused. Over time, fresh nutrient solution is added, the nutrient solution is replaced, or the solution gets tested and amended to correct nutrient imbalances. In open systems, the nutrient solution is not reused.
The major water-based systems include nutrient film technique (NFT), deep water culture (DWC) and aeroponic. Key factors of water-based systems are compared in Table 2, with systems listed in ascending order.
Growing media-based systems use media placed in plastic buckets or plastic/fabric bags which can be used in Dutch bucket (also called bato bucket), ebb-and-flow and wick/mat systems. NFT, DWC, Dutch bucket and grow bags are commonly used by commercial vegetable farms.
Table 2. Comparison of water-based hydroponic systems.
Factor | Systems in ascending order |
---|---|
Water and fertilizer use | Aeroponics (lowest use) → NFT → DWC (highest use) |
Construction cost and complexity | DWC (least) → NFT → Aeroponics (greatest) |
Plant loss risk due to clogging/leaks | DWC (least loss risk) → NFT → Aeroponics (most loss risk) |
Ease of nutrient system management | Aeroponics (least complex) → NFT → DWC (more complex) |
Nutrient film technique (NFT)
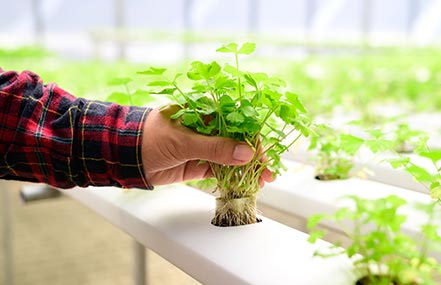
Lettuce, herbs and strawberries are commonly grown using nutrient film technique. In NFT systems, the roots of the plants extend into a plastic pipe, tube or trough (Figure 2). The troughs must be placed at an angle of 1 to 2 percent (0.12-inch to 0.24-inch per foot). Nutrient solution flows continuously over the roots. Aeration is not needed because the solution is so shallow that roots are exposed to the air and oxygen easily diffuses and dissolves in the nutrient solution.
The NFT uses less water and fertilizer than DWC. Adjusting solution pH and temperature is easier than in other systems. Management concerns include monitoring driplines for leaks and clogs. If water pumps fail, or if driplines clog, plants may immediately wilt.
Deep water culture (DWC)
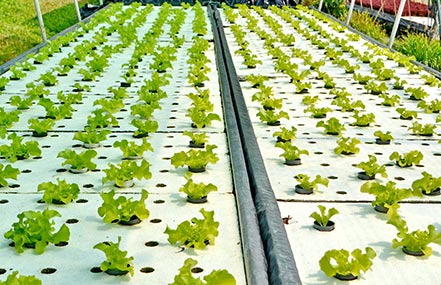
The deep water culture system is also called the floating raft because plants are usually positioned in floating polystyrene panels (Figure 3). The name “deep water” can be misleading, as the water depth only needs to be a bit deeper than roots. Common recommended depths are 4 to 12 inches.
Leafy greens and herbs are crops commonly grown in DWC. A support structure, such as plastic net cups, keeps the plants upright. Commercial systems will often size the holes to fit the plant plugs without the need of plastic cups. Deep water culture requires simple aeration pumps to supply additional oxygen to roots; however, the plants will not immediately wilt if pumps fail.
A DWC system can be the simplest and least expensive hydroponics system to establish, but water and fertilizer usage are greater over time compared to other systems. It can also be more costly to adjust the temperature, pH and dissolved oxygen levels in a DWC system. However, DWC is more resilient and forgiving for beginning farmers because the plants will not immediately wilt if an aeration pump fails.
Aeroponics
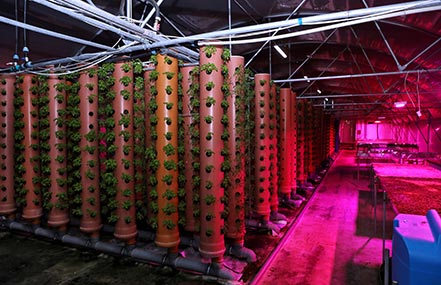
Aeroponics can be used for leafy greens and herbs. There is no need for aeration, and it requires less water than NFT and DWC systems. In aeroponic systems, plant roots are suspended in the air and exposed to the nutrient solution through microsprinkler or fogging nozzles. The roots need to be continuously exposed to the nutrient solution to prevent plant wilting. Aeroponic systems can be built vertically, which increases design and space possibilities (Figure 4).
Drawbacks to aeroponics include the need for pressurized irrigation systems and high-quality water that will not clog misters. If the pumps fail or emitters clog, the aeroponics system will fail and the plants will immediately wilt.
Dutch bucket
The Dutch bucket system is ideal for tomatoes, cucumbers and other vining or fruiting crops. Each plant grows in a container containing growing media. Trellis systems are used to support the plants. The greenhouse structure and trellis wire must be able to support the weight of the plants. The trellis wire must be able to support at least 20 pounds per foot of wire. Dutch bucket systems are some of the most common hydroponic systems around the world.
The type of growing media determines irrigation frequency. There is great variation in availability, costs and quality of growing media. Common media are perlite, coconut coir, rockwool, potting mixes, gravel and expanded clay pellets.
Nutrient solution is delivered to each container through drip irrigation systems. The nutrient solution then passes through the media and drains back into a nutrient solution reservoir. Growing media containing organic matter, like potting mix, will require more intensive management for pH. It is safe to assume that the pH of the rootzone will be similar to the pH of the nutrient solution with inorganic growing media. For growing media with organic matter, the nutrient solution will interact with the organic matter and microorganisms, changing the pH of the rootzone.
Grow bags
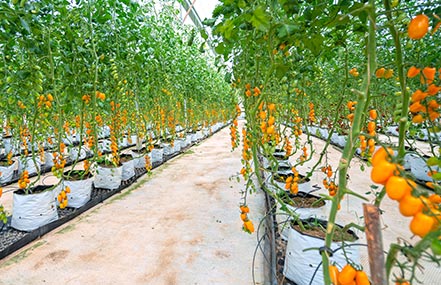
Grow bag systems are similar to Dutch bucket systems. Polyethylene bags, set closely together, are filled with a potting mix, like vermiculite-peat. Nutrient solution is delivered to the bag using drip tubing (Figure 5). The bags can be used for multiple plants before replacement is needed.
Grow bags are cheaper to purchase than Dutch buckets. Grow bags can be disposed after the crop cycle. Dutch buckets need to be washed and sanitized between crop cycles, which increase labor costs. A disadvantage of grow bags is the amount of waste generated. Some consumers may perceive grow bag systems as lacking sustainability by not reusing plastic materials.
Aquaponics
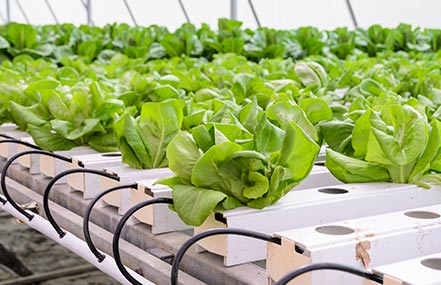
Aquaponics combines hydroponic systems with aquaculture. Fish are produced in indoor tanks, and beneficial microbes in biofilters/bioreactors convert fish wastes to fertilizers that can benefit plants grown hydroponically (Figure 6). There are many designs of aquaponics systems, depending on the fish species and crops raised. They can be set up as coupled (water recirculates between the fish rearing, biofilters and hydroponic units) and decoupled (the water does not return to the fish unit after it exits the hydroponic unit) systems.
Aquaponics generates much attention because of the system’s capacity to produce both plants and fish protein. However, aquaponics systems may require relatively high fish prices for profitability. Aquaponics also requires advanced management and production skills in both hydroponics and aquaculture.
Environmental control systems
CEA hydroponic production relies on various environmental control systems to keep plants in their comfort zones to maximize productivity. The main systems involve managing air temperature, relative humidity, concentration of carbon dioxide in the air, light and the nutrient solution.
Outside weather
The weather outside can greatly affect management decisions for hydroponics production inside the greenhouse. Temperature and natural light availability will vary according to season. Environmental control systems are how a hydroponic producer manages for optimal production and economic efficiencies.
Heating, cooling and relative humidity
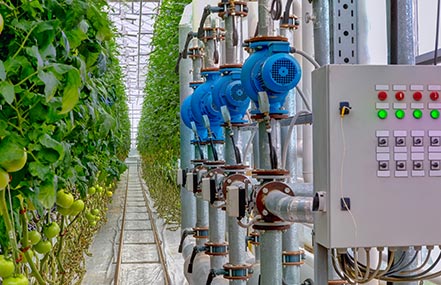
Temperatures inside a greenhouse fluctuate without environmental controls. Heaters, fans and other temperature control systems are required. A general temperature range for mixed crop hydroponics production is 65 F to 75 F. Plant health decreases significantly when temperatures range above 85 F. Automated systems can decrease labor needed to keep plants at ideal temperatures (Figure 7).
Systems used for cooling and heating the greenhouse may also help with air circulation and managing relative humidity levels. Relative humidity regulates water uptake and impact disease pressure. Most hydroponic facilities are maintained between 50 and 60 percent relative humidity for plant health. Ventilation and air circulation systems are needed so that humidity does not reach levels that reduce plant growth and health. Sensors and automated systems are also available to control relative humidity.
Lighting
Lighting in hydroponic systems may rely on natural sunlight, artificial lights supplementing natural sunlight, or completely rely on artificial lights. The plants will need approximately 12 to 16 hours of light per day. Artificial light can be used to supplement sunlight in greenhouses or provide all light needs in full indoor systems. High pressure sodium (HPS), fluorescent, and light emitting diode (LED) lights are commonly used in hydroponic systems. Light sensors and timers can increase energy efficiency and optimize crop yields.
There is a direct relationship between energy efficiency and the initial capital investment in lighting systems. The HPS systems require the lowest initial investment but are the least energy efficient option and have the shortest life. LED systems usually require the higher initial investment but are the most energy efficient and have a longer useful life. LED lights, the most versatile of the three systems, have an additional benefit in that they can be customized to deliver specific light recipes. Fluorescent lights sit in between HPS and LED in terms of initial investment, energy use efficiency, and lifespan. LED systems are the most versatile of the three systems.
Nutrient solutions
Water and fertilizers make up the solutions that deliver a nutrition program to plants grown hydroponically. The nutrition program purposes are these:
- Provide all essential elements
- Provide optimal quantities of these elements for plant growth
- Promote availability and absorption of nutrients
Managing nutrient solutions begins with knowing the quality of your water source. It is important to get your water tested to determine if it is suitable or if it needs to be treated before establishing a nutrition program. The laboratory should test water for:
- pH
- Macronutrients (nitrogen, phosphorous, potassium, magnesium, sulfur)
- Micronutrients (sodium, chloride, iron, manganese, boron, copper, zinc, molybdenum, aluminum)
- Electrical conductivity (EC)
- Alkalinity
- Total suspended solids
- Total bacteria counts (optional)
- E. coli (to comply with certification requirements and the Produce Safety Rule)
- Turbidity (optional)
- Particle size distribution (optional to determine filtration needs)
Careful measurement and mixing of water soluble fertilizers is required to ensure plants receive proper nutrient levels. Nutrient requirements will differ among plant species and growth stages. Macronutrient and micronutrient requirements are reported in parts per million (ppm), equivalent to milligrams per one liter of water (1 ppm = 1 milligram/liter).
Adding nutrients will impact water quality characteristics, and it is important to measure changes in pH and electrical conductivity and make adjustments after making nutrient solutions. Adjustments may also be needed based on plant health, pests and disease pressures. The grower must have a monitoring program to make adjustments to keep the nutrient solution adequate for the plants.
Producers must have the knowledge and skills necessary to adjust water quality and nutrient solutions. The products that are readily available, as well as the production system and available equipment, will determine the process used to make the nutrient solution. You may contact Juan Cabrera-Garcia or your local extension specialist to evaluate your water source and create nutrient solution recipes that matches your operation.
Since plants are continually using water and nutrients, the properties of the nutrient solutions used in hydroponics will change over time. The following is a general guideline for managing nutrient solutions:
- Test your water source.
- Research nutrient requirements for your crops (nutrient levels and pH).
- Calculate how much fertilizer you need for the nutrient solutions.
- Prepare nutrient solutions.
- Measure pH and EC.
- Adjust the pH as needed.
- Constantly measure and adjust the pH and EC of the nutrient solution.
Structures
Greenhouses are typically used for hydroponic systems. However, hydroponics may be used in high tunnels and structures closed to natural light. The production location, availability of existing structures, and cost of establishing new structures can all determine suitable options for hydroponics. As of 2024, the cost of greenhouse structures (with environmental control systems) ranged from $10 to $25 per square foot. The cost can double for installation. It is important to shop around for greenhouse suppliers and installation contractors.
Summary
Controlled environment agriculture can produce vegetables and fruits in situations and seasons when field production is impossible. Hydroponics production helps meet year-round demand for fresh produce. Well-managed hydroponic systems could help producers respond to some market demands for certain crops. While hydroponic systems vary based on the type of system and available equipment, regular attention to crop health and monitoring the nutrient solution supply is essential.