On-farm manure treatment can be challenging for many animal feeding operations, especially for those who have limited nearby fields for manure land application. To date, very few large-scale animal farms utilize composting as a long-term treatment for liquid manure.
Composting is a biological process in which microorganisms convert organic materials into soil-like material, which can effectively convert animal manure into value-added products. Compost has been well-documented and proven to be an excellent soil conditioner, which could add organic matter, improve soil structure, reduce fertilizer requirements, and reduce soil erosion potential.
Composting has been occurring naturally for millions of years. The major difference between the natural process and the managed form is in managing the operational parameters and balancing the raw materials (feedstocks). The controlled-composting process is affected by several factors, such as ambient temperature, duration of different thermal phases, inoculum concentration (if any), moisture content (MC), carbon/nitrogen (C/N) ratio, oxygen concentration, turning frequency, pH, particle size, and characteristics of the bulking agent. Under controlled conditions, composting is accomplished in three main phases: rising temperature, stationary phase, and cooling phase. In addition, curing is a critical but often neglected stage of composting. In addition to helping in compost maturation, curing further allows the aerobic decomposition of resistant compounds, organic acids, large particles, and clumps of material that remain after active compositing.
There are several common types of composting technologies used in manure composting, including windrow composting, static pile, aerated pile, mixing-vessel, and in-vessel.
The mixing-vessel and in-vessel composting are collectively known as methods that confine the composting materials within a building, container, pit, or vessel and rely on various forced aeration and mechanical turning techniques to speed up the composting process. As a result, mixing-vessel and in-vessel composting can be more efficient (short composting period) than the other composting methods, including passive and windrow composting.
Compost-A-Matic is a composting system that routinely mixes and aerates compost materials in concrete pits. The composting systems offer both options of continuous flow composting (adding material in the compost pit daily) and batch composting (filling the entire pit with material only once, and turning/aerating the material until composted). However, the continuous flow option is more popular due to the simplicity of adding organic material frequently. A 7-foot-long pit (channel) space is created at the front end, and organic material is added every time the compost turner mixes and turns the compost. Limited livestock farms, especially commercial pig farms, have routinely used mixing-vessel composting systems to manage their manure. The purpose of this case study was to highlight some aspects of system design, operation, and management of a mixing-vessel composting system at a large swine finishing farm.
Swine farm and composting facility
The mixing-vessel composting system was used at a commercial swine farm that was located in the Midwest and treated the manure produced by up to 24,000 head of finishing swine. There were four identical wean-to-finish barns with at least 5 weeks of age difference, and each barn had four identical rooms housing 1,500 heads of swine each, Figure 1. A confined facility was built for the swine manure treatment with a mixing-vessel composting system: Compost-A-Matic. The layout of a section of the farm and a detailed plan sketch of the composting facility is shown in Figure 1.
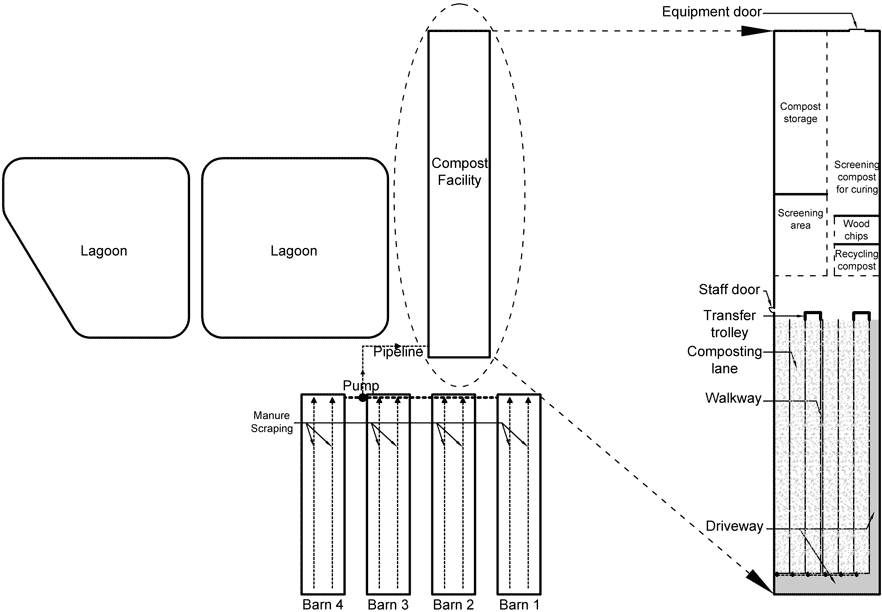
A manure scraper system removed the swine manure under the slatted floor, in a shallow gutter system without requiring excess water. The manure scraping time of the swine barns was typically once or twice per day and can be flexible according to the manure production and composting operation. Scraped manure from the four barns was collected into a centralized collection pit. The manure was then pumped through a lift station and pipeline to the composting facility. In case of failure of the manure composting system, two lagoons were also available on the farm. A 3-ft wide walkway was included between the third and fourth composting pit row for maintenance and aeration pumps and pipes. A 15-ft wide driveway for the front-end loader to bring the carbon materials was included in the southeast side and south end of the composting facility, Figure 1.
Previously, a sloped screen separator (Key Dollar, Parkville, Missouri) was used to reduce some of the water in the manure before pumping it into the composting channels, but the screen separator was not appropriately sized and was abandoned. It is noted that biosecurity is a major consideration in the design and operation of composting systems and that a Danish entry system was used to ensure a line of separation for the composting facility.
The dimensions of the composting facility were appropriate, 800 ft × 150 ft × 20 ft (length × width × sidewall height). The height of the sidewall was designed to accommodate the height of the front-end loader. The composting facility was designed and constructed as a steel frame. The internal space was divided into two parts of almost the same size by the staff door, one side is used for the composting lanes, and the other side is used for the follow-up operations, including screening, curing, and storage (shown in Figure 1).
The composting barn was built in 2011, and no contractor was used. In 2021, the process produced 7,500 yards3 of compost from all the manure from the finishing barns with 24,000 heads.
Mixing-vessel composting principal
The mixing-vessel compost system utilizes a shallow pit design to biologically stabilize organic material with/without forced aeration. The commercial provider for the composter is Aggero, LLC., a newly named waste management division of Farmer Automatic of America, Inc. The company is located in Statesboro, Georgia, and specializes in animal farm equipment, especially for the poultry industry.
A continuous flow composting mode was selected in the swine farm, and the mixing-vessel composting process is presented in Figure 2. A Compost-A-Matic 610M agitator was used to mix and move the compost forward daily and to create space near the front end of the compost pit by the manure inlet for loading the scraped manure and woodchips.

Typically, consistent and good quality compost starts with blending raw materials to maintain a C/N ratio of 25:1 to 30:1, which is commonly believed to be the ideal range for active composting. In this mixing-vessel composting system, fresh woodchips were used as a carbon source due to their local availability. Local urban wood waste was converted into woodchips using a tub grinder with a mesh size of two inches. At the rear end of the compost pit, the compost was screened using a mesh size of two inches and separated into finer compost and coarse compost. The finer compost was then moved to a pile for curing, and the coarse materials were added back (recycled) to the pit rows along with fresh woodchips for further composting. The swine farm’s compost formula included one scoop (approximately 4 yard3) of fresh woodchips, two scoops of coarse (screened) compost, and one scoop of fine compost. The fine compost was added to help provide the microbes to enhance the composting process. The volume ratio of the raw swine manure and carbon materials was about 1:1. After about 55 days of mixing and composting, the compost became less moist and was screened for either adding back to the pits for composting or piled for curing.
On-farm mixing-vessel composting system design and operation
A rational design of the swine manure mixing-vessel composting system should begin with estimating the total manure production and frequency of manure removal and addition to the composting system. The composting pit rows must be designed to match the manure production and fluctuations and emptied frequently to accommodate the newly scraped manure from the pig barns, which have only minimal space for temporary manure storage. In addition, the facility needs to include appropriate space according to its function, including fresh carbon sources, composting, screening, curing, and storage areas, and to allow movement of the needed equipment and to maneuver the transfer trolley.
System design and operating capacity
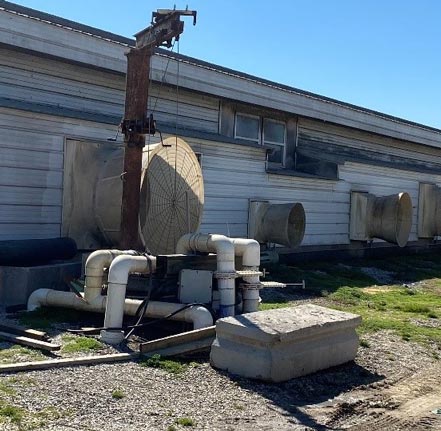
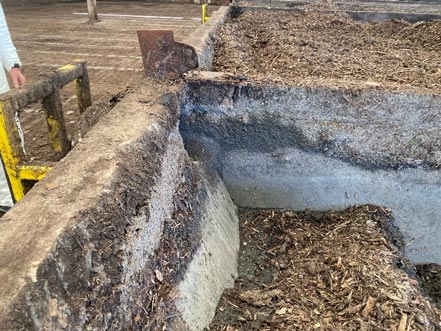
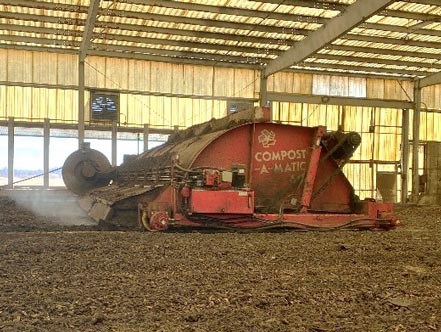
Initially, this system was designed to process manure from three wean-to-finish with a total capacity of 18,000 head, but the system actually handled manure from four barns, with a total capacity of 24,000 head. The daily manure production of the 18,000 (or 24,000) head of wean-to-finish swine was 2,520 (or 3,360) ft3 assuming that the manure production per pig is 0.14 ft3/d (ASABE standard). Manure is first scraped from the barn daily (except on Sunday) and pumped via a lift station (Figure 3) through an underground pipeline to the composting facility and composting pit rows (Figure 4).
The width and depth of the concrete pit rows were designed and constructed according to the agitator sizes. For this composting site, two Compost-A-Matic 610M agitators (Figure 5) were used to mix and aerate the mixture of manure and carbon materials, each for three composting pit rows, respectively. A total of six composting pit rows with dimensions of 300 ft × 19.6 ft × 3.3 ft (length × width × depth) were built in the composting facility (Figure 1). The length and number of composting rows are designed to accommodate the daily manure production, carbon materials, and MCs.
Each time when the mixing vessel mixed the compost, an approximate space of 7 ft was created at the front end of the pit row, creating about 432 ft3 of space for new manure and carbon material addition. There was approximately 4,320 ft3 of space available per day for manure and carbon material addition, considering each compost mixer can mix and aerate five turns of the compost pit rows when the farm crew was working 18–20 hours per day. The time needed to mix each pit row was determined by the length of the compost pit, which was affected by the MC variation. The farmer reported that the compost loses MC faster during warmer than colder months.
The daily manure production of each 1,000-head finishing swine is approximately 170 ft3 (ASABE standard). Therefore, the mixing vessel size and unit number selection should provide at least 170 ft3 of treatment capacity daily. For example, for a smaller pig farm of a 4,800-head finishing swine operation, one could use only a unit of Compost-A-Matic 310 agitator and a unit of transfer trolley while using half the width of the compost pit row, and adjusting the pit length, the number of pit row, and farm staff shift hours accordingly.
Composting system operation
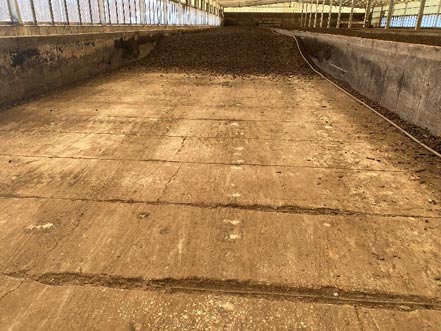
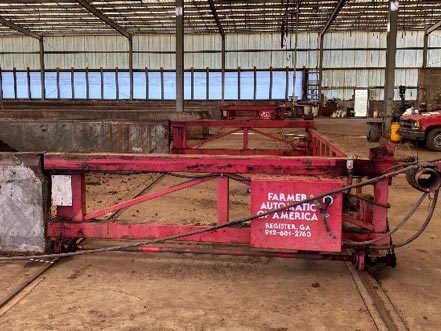
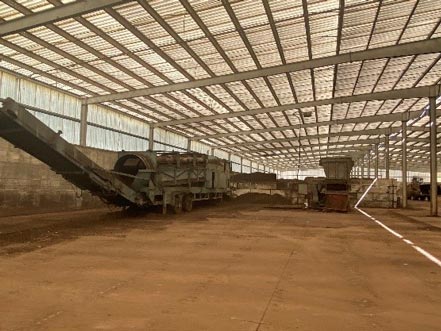
Composting is an aerobic process which consumes large amounts of oxygen. The mixing-vessel system advances through the compost rows to provide turning and aerating. This process also moves older material to the rear end of the pit, continuously advancing the compost substrate until becoming a more stable compost product. During this mixing/moving process, the mixing paddles break up large particles to allow maximum surface area for oxygen contact. In addition to providing oxygen, the turning and aerating could also remove heat, water vapor, and other gases trapped within the composting piles.
The air supply pipeline at the bottom of the lanes (Figure 6) was initially designed to help aerate the compost, enhance the decomposition, and potentially shorten the time required. However, the air supply pipeline’s air outlet holes were easily blocked, and the mixing vessel was found to be able to provide enough aeration, thus, the aeration system was eventually abandoned in the early stage of the composting process.
Turning the compost once or twice every day was reported to be sufficient for compost aeration needs and heat removal. The workers generally turned the compost twice (once per day), making enough space to accommodate the daily produced manure from the four barns. Almost four hours were required for the mixing vessel to turn a full 300-ft long composting row. The composting facility was operated on two 10–12 hours shift schedules per day.
The mixing vessel was designed to mix each of the three pit rows once a day. After that, the agitator was shifted to another composting row via a transfer trolley (Figure 7), which was designed to enable one mixing-vessel system to serve three pit rows separated by the center walkway. To minimize the trolley transfer time, the farm crew often programmed the mixing vessel to repeat mixing the same pit, thus, some pit rows were mixed twice daily. The composting facility typically operates six days a week. Therefore, the manure was not scraped in the swine barns on Sundays.
Urban waste wood was collected from a nearby city and was used to prepare fresh woodchips using a tub grinder. The woodchips were ground and screened at a nearby field before being moved to the composting facility. After the initial composting within the concrete pit rows, or after about 55 days (depending on the feedstock MC and season) of composting, the compost was screened and divided into coarse recycled woodchips and fine compost for either recycling into the composting process or moved into another section to be cured (Figure 8).
The composting system also worked as a dehydration system. The material was allowed to stay about 55 days in the composting rows to achieve 35–45% MC of the substrate. During composting, moisture levels change as water evaporates and a beginning MC of 40–65% is a general recommendation that works well for most of the materials. At MC of less than 40%, the microbial activity slows down, whereas, at a MC above 65%, water displaces much of the air in the pore space of the composting materials, limits air movement, and subsequently leads to anaerobic conditions. According to the farm, the MC of the pig manure is about 90–97%. Therefore, blending the raw materials reduced the original MC of composting substrate. In addition, the building helped with maintaining room temperatures during winter months. However, the compost yield was still twice as much in the summer as compared to the winter.
Part of the screened, finer compost was moved to different piles for curing. Curing continues until the MC reaches 30–35%, it was reported that the inside temperature of the curing piles could still reach 120–130°F. The farmer also stated that the goal was to maintain the finished compost to have a MC of around 30% to minimize the dust during moving and spreading (land application) in the field.
The paddles of the mixing vessels were typically changed out every five weeks, which are typically made in the farm’s shop. A staff member maintained the equipment at least once or twice a week at the swine farm. The electrical system was typically the most problematic part due to the relatively moist and corrosive environment. It was also reported that electrical maintenance was also the most expensive labor, usually $50+ per hour, and required a little more planning for biosecurity reasons because the electrician also worked on other parts of the farm.
The ventilation system of a confined building such as the composting facility is vital to maintain good air quality and thermal conditions inside. In the swine farm composting facility, natural ventilation with sidewall curtain openings (in the sidewall along the composting rows) and a ridge vent (through the longitude of the whole building) were used when the inside temperatures were above 85°F. When the inside temperature dropped below 85°F, the barn was switched to negative-pressure ventilation automatically. The controller turned on a total of eight exhaust fans (36” diameter) installed on both the end wall and sidewalls of the composting barn. The ventilation fans were helpful in removing a significant amount of gases, moisture, and dust in the air.
Characteristics and nutrient changes during the composting process
The MC and C/N ratio are the most important factors affecting composting. During our visit to the composting facility, samples were collected from the fresh carbon material, screened composts, cured compost, and five locations which are uniformly distributed along with the compost pit row (length 00, length 02, length 04, length 06, and length 08, (Figure 9). As expected, MC decreased gradually along the compost row, indicating the composting process with mixing was able to evaporate a significant amount of moisture. Eventually, the MC of screened finer compost dropped to below 40%, while the MC of cured compost decreased to 27.2%. Meanwhile, the MC of the recycling compost was lower than the fresh woodchips, and the mixed substrate at length 00 (starting day). The C/N ratio of new woodchips was more than 80, indicating that woodchips were an appropriate substrate as a carbon source. Again, the C/N ratio of the recycling compost was lower than the new woodchips but higher than all other substrates, including the screened and cured compost.
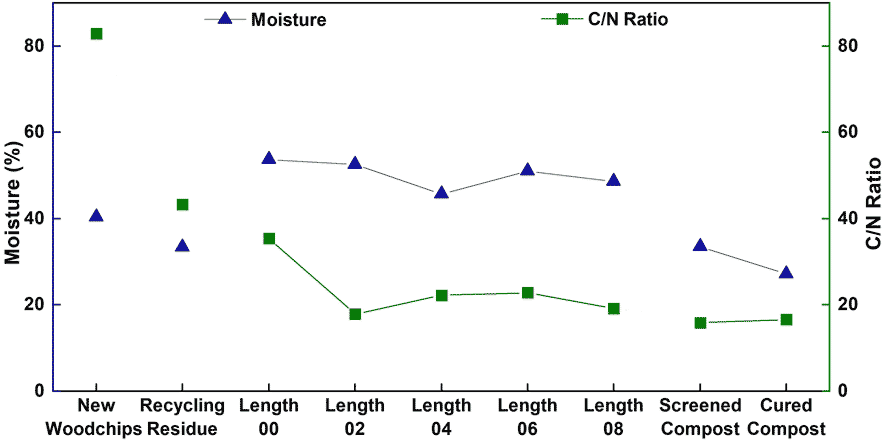
Compost prices are often determined by the essential nutrients, total nitrogen (N), phosphorus (P), and potassium (K) values. The N, P, and K concentrations of all collected samples were also measured and are presented in Figure 10. The N, P, and K concentrations of the new woodchips were the lowest. This is expected because of the manure addition, and the N, P, and K concentrations of the substrate would increase slightly when the compost shrinks and dries. Thus the N, P, and K concentrations of the cured compost were shown to be the highest. Evidently, the N, P, and K concentrations were found to be closely correlated to the MC values of the different composting stage samples.
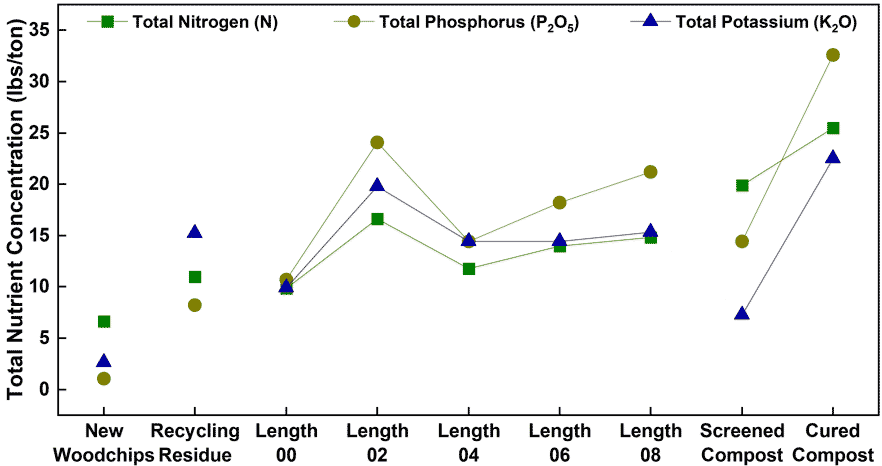
Compost quality and economic evaluation
Compost quality can affect the price and amount needed for land application, meaning that finished compost analysis is often needed to verify product safety and market claims. According to U.S. composting council, the American Society for Testing and Materials (ASTM) is the agency that publishes Test Method for the Examination of Composting and Compost (TMECC) to provide detailed protocols for verifying the physical, chemical, and biological conditions of composting feedstock, material in process and finished compost products at the point of sale. More routine analysis would be needed if the compost were to be sold as bagged compost products.
Important characteristics and considerations
In addition to the major nutrients (N, P, and K), other characteristics including pH, soluble salt, moisture, organic matter, particle size, maturity, stability, heavy metals, insects, and pathogens, can also impact the quality of compost. As pH is the measure of hydrogen ion activity, compost can affect the pH of the soil or growing media depending on the amount of compost applied. Soil pH is often adjusted by using materials such as lime (to raise pH) and sulfur (to lower pH), which could also be used to adjust the compost product.
Soluble salts in compost refer to the amount of soluble ions in a solution of compost and water. Although plant species have a salinity tolerance, excessive soluble salts can cause phytotoxicity in plants. Typical conductivity values in soil range from 0 to 1.5 in most areas of the country, whereas most composts have higher salt conductivity. Therefore, watering could be used to reduce the soluble salt content in the soil.
Typically, MC of 40–50% is recommended for finished compost. Very dry compost (35% MC or below) can be dusty and irritating to work with, while very wet compost (55–60% MC and higher) can become heavy and clumpy, making its application more difficult and delivery more expensive.
Maturity is the degree or level of completeness of composting. A single property does not describe maturity, and therefore, maturity is best assessed by measuring two or more compost characteristics. Some immature composts may contain high amounts of free ammonia, certain organic acids, or other water-soluble compounds, which can limit seed germination and root development or cause odor. All uses of compost require a mature product free of these potentially phytotoxic components. The stability of a given compost is important in determining the potential impact of the material on nitrogen availability in soil or growth media and maintaining consistent volume and porosity. Most uses of compost require a stable to very stable product that will prevent nutrient tie-up and maintain or enhance oxygen availability in soil or growth media.
Certain heavy metals and trace elements (e.g., boron, manganese, molybdenum, nickel, and selenium) are also known to cause phytotoxic in plants, and specific plant species are known to be more sensitive than others. However, these elements are not typically found in compost in detrimental quantities. All composts containing regulated feedstock must meet national and state safety standards before being marketed. In addition, the U.S. Composting Council’s Seal of Testing Assurance (STA) certified compost must meet the EPA testing limits for heavy metals.
Pathogens are disease-causing organisms, including bacteria, viruses, fungi, helminths, and protozoa which may be present in raw wastes or by-products. Both plant and human disease-causing pathogens are present at some background levels in the environment. The composting process must eliminate or reduce pathogens to a level that is below the threshold where the danger of transmitting diseases will occur. The time-temperature requirement ensures plant and human pathogen destruction in compost and is considered an effective means to determine that compost is relatively weed-free. The U.S. Composting Council’s Seal of Testing Assurance (STA) certified compost must meet the EPA testing limits for pathogens.
Economic evaluation
The swine farm management constructed the composting barn themselves in 2011. The composting facility and equipment costs totaled $2.5 million, with an equal cost for each. It is very likely that the same facilities and equipment would cost more today and be built using contractors. A recent quote (September 2022) for the Compost-A-Matic 610M agitator was $200,000. The farm manager estimated that the construction cost of the composting facility would be 30% higher today.
The market price of the compost is $35–$40 per yard, according to the farm manager, which is typically priced based on the N, P, and K values. There is, however, competition from chicken litter which often has higher N, P, and K concentrations as crop fertilizer. Researchers from a nearby land-grant university evaluated the composting products and estimated that the compost was valuable due to the soil amendment quality and beneficial bacteria and humic acids. The farm has been selling some of the compost in bulk. The finished composts are primarily land applied to the farm’s 500–700 acres, where they are used as soil amendments, and were especially helpful to the edges of the fields where manure was not applied.
Table 1. Estimated compost income and expenditures for the composting facility on an annual basis.
Income/Expense | Unit | Amount |
---|---|---|
Compost production | yard3 | 7,500 |
Unit Price | dollars per yard | $35 |
Potential compost income | dollars per year | $262,500 |
Number of employees | - | 2 |
Unit-payment | salary per person | $48,000 |
Total employees expense | dollars | $96,000 |
Electricity amounts | kW·h | 184,392 |
Unit-price | dollars per kW·h | $0.10 |
Total electricity expenses | dollars | $18,439 |
Fuel amounts | gallons | 14,976 (diesel) |
Unit-price | dollars per gallons | $3.30 (diesel) |
Total fuel expenses | dollars per year | $49,421 |
Fresh woodchip costs | dollars per year | $75,000 |
Parts and supplies | dollars per year | $30,000 |
Maintenance cost, electrical | dollars per year | $5,000 |
Total annual costs | dollars per year | $273,860 |
Estimated annual expenses for the composting facility are listed in Table 1. All the values were estimated following the known operating and maintenance costs. The higher costs were labor, fresh woodchips, and fuel, about $96K, $75K, and $48K, respectively, in 2021. Each of the mixing vessels was equipped with two 10-horsepower agitator motors and a lift/propel motor rated at 2 horsepower. Assuming both mixers operate for 18 hours per day, this is equivalent to 18 hours of operation for 44 horsepower motors (2 × 22 horsepower) each day. This leads to an electrical need of 591 kW-h/day, with an estimated cost of $59.1 for daily operation, assuming an electricity cost of $0.1/kW-h. Extrapolating this to a yearly cost, results in $18,439 a year, assuming six working days for the 52 weeks per year.
Fuel consumption was estimated, assuming the front-end loader was operating for 8 hours per day at 4 gallons/hour of diesel, which is 32 gallons of diesel per day. The screening machine was operated for 2 hours per day, at 8 gallons/hour of diesel, which is 16 gallons of diesel per day — totaling to 14,976 gallons of diesel per year or $49,421/year of diesel for moving the fresh woodchips and compost products and compost screening.
These costs do not include the carbon materials needed. The farm estimated the cost of making the fresh woodchip at $5/yard3. The farm was estimated to produce 7,500 yard3 of finished compost per year. Assuming the compost substrates shrink by 50% conservatively, the fresh woodchips needed could be
as much as 15,000 yard3. Thus it can be estimated that the fresh woodchips would cost $75,000/yr. If a farm were to purchase woodchips from a supplier, the cost would depend on the locations (distance and transportation costs) and supplies of locally available woodchips. The typical woodchip costs range from $15 to $35/yard3. The estimated total annual costs to operate the mixing-vessel composting system is thus $274K/year ($18.4K electricity + $49.4K fuel + $75K woodchips + $30K parts/supplies + $5K electrical maintenance + $96K labor).
The estimated value for the finished compost was $262,500/year. This value is estimated based on the average compost production of 7,500 yard3 and an estimated value of $35/yard3, Table 1. The costs of the compost building and equipment (composters, front-end loaders, compost screening machines, etc.) are not included in the table. Amortization of the building and equipment would be affected by the lifespan and original conditions (some of the equipment were bought used). The costs of the land application of the compost were also not considered. The cost of installing and operating the mixing-vessel composting system was more expensive than the potential woodchip income based on the current market value.
Conclusions
A mixing-vessel composting system combined with an automatic manure scraper system, and when relatively inexpensive woodchips are available, can efficiently convert the swine manure into valuable compost without producing wastewater. Woodchips work very well as a carbon source due to their high C/N ratios and longer decomposition time, as the hardy woodchips can be screened and recycled in the composting process. Daily mixing seemed to provide enough aeration for the compost pit rows and did not require the pipeline forced-air system, which was easily blocked and required more maintenance.
The compost pits must match the agitator size, and the number of pits and agitators needed depends on the farm size and daily manure production, which also determines the composting facility and necessary equipment to move and screen the compost and carbon materials. In addition, a well-designed ventilation system combining mechanical and natural ventilation are essential to maintain good air quality and thermal conditions inside the compost barn. Finally, the compost value depends on total N, P, and K concentrations and the market price of the fertilizer. Mixing-vessel composting can be costly and labor-intensive, but it has several benefits. It reduces the need for long-term liquid manure storage and eliminates the need for agitating and applying large amounts of deep-pit manure or lagoon effluent on the land. This can be especially useful for animal farms that are landlocked and facing manure nutrient management challenges.
Finally, based on the farm size and manure production, a smaller unit of the mixing vessel and custom-design composting barn could be fitted to a finishing pig farm as small as 4,800-hd. Such a composting system combined with a manure scraper system can alleviate the manure pressure by eliminating all the liquid manure and produce good quality compost products.
Disclaimer
Mentioning the product model, brand name, and information in this publication are solely for readers’ general interest and convenience and do not suggest any endorsement by the authors and the University of Missouri.
Acknowledgment
The authors appreciate the help of the farm management team and local extension faculty.
References
- ASABE D384.2 MAR2005 (R2019). Manure Production and Characteristics. In: ASABE STANDARDS, ASABE. St. Joseph, MI 49085-9659
- Golueke, C. G., & Diaz, L. F. (1990). Understanding the basics of composting. Biocycle, 31(4), 56–59.
- Gondek, M., Weindorf, D. C., Thiel, C., & Kleinheinz, G. (2020). Soluble salts in compost and their effects on soil and plants: A review. Compost Science & Utilization, 28(2), 59–75.
- Iowa State University. (2016). How To Change Your Soil’s pH.
- Rynk, R., Van de Kamp, M., Willson, G.B., Singley, M.E., Richard, T.L., Kolega, J.J., Gouin, F.R., Laliberty, L., Kay, D., Murphy, D. and Hoitink, H.A., (1992). On-farm composting handbook (NRAES 54). Northeast Regional Agricultural Engineering Service (NRAES).
- Seal, A., Bera, R., Chatterjee, A. K., & Dolui, A. K. (2012). Evaluation of a new composting method in terms of its biodegradation pathway and assessment of compost quality, maturity, and stability. Archives of Agronomy and Soil Science, 58(9), 995–1012.
- US EPA. A plain English guide to the EPA part 503 biosolids rule (PDF).
Reviewed by Joseph Heywood Harrison, Professor, Nutrient Management Specialist, Washington State University, and Lide Chen, Associate Professor, Nutrient Management Specialist, University of Idaho.