Editor’s note
See the Forage Irrigation System Cost Analyzer (downloadable Excel workbook) for related information.
Irrigation presents an opportunity for Missouri forage producers to mitigate production risk from drought and improve forage yield. This guide explores three considerations before choosing a forage irrigation system: expected forage response, irrigation system options, and the economics of irrigating forage.
Factors in choosing a system
Each producer’s irrigation situation is unique. Site-specific research will determine if investing in forage irrigation would be a good economic decision. The following factors should be considered.
Hydrology, topography and geology
In most areas in Missouri, water availability affects both the decision to irrigate and how many acres can be watered. Carefully evaluate existing surface and groundwater resources. Determine how much water can be withdrawn and what rate (gallons per minute) can be withdrawn. Investigate the reliability of sources during prolonged droughts. If necessary, evaluate the cost of developing a new water source, such as a well or lake.
Land that is highly sloped may not be conducive to irrigation systems. Oddly-shaped fields may allow only certain irrigation systems to be an option. Soil types affect the rate of water absorption, potential for forage growth and potential for water runoff. Soils determine the total amount of water that will need to be applied, how much water will need to be applied per pass and how often water will need to be applied.
Energy cost and availability
The cost of running power units to pump water can vary greatly. Wells that lift water from a deep source or irrigation systems that require significant pressure can increase the cost of pumping water. Fields without access to electricity will need a different energy source, such as diesel or propane.
Labor
Each irrigation system has labor requirements. Center pivot systems require less daily labor than manually moved systems such as a traveling gun or pod-line irrigation. You need to have enough labor available and understand its cost.
Irrigation system cost and return
Farmers invest in irrigation seeking an economic benefit. Information to evaluate the costs and returns of forage irrigation can be found later in this guide.
Forage response for irrigation
In Missouri, the greatest moisture deficit for most forage crops is from June through August. Rapid growth stages for forages represent times of the most forage yield improvement from irrigation if rainfall is inadequate. Figures 1 and 2 demonstrate growth patterns and periods for efficient irrigation for cool-season and warm-season perennial forages.
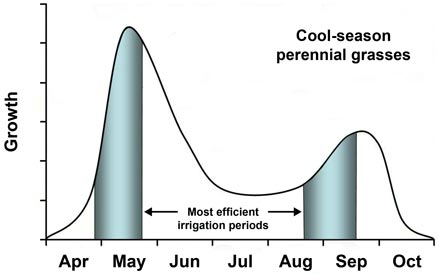
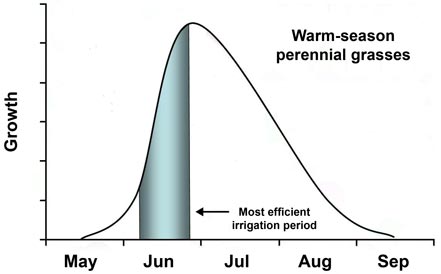
Note that, for cool-season species, rainfall is often adequate when temperatures are ideal for growth. Unfortunately, most producers interested in irrigating cool-season grasses want to extend growth into the summer when temperatures are less than ideal for maximum growth and, thus, irrigation efficiency. Further, forage species vary in how effectively they convert irrigation water into additional forage (Table 1).
Table 1. Missouri guidelines for forage response to irrigation.
Species | Pounds of dry matter per acre-inch water* |
---|---|
Cool-season perennial grass | 450 to 700 |
Warm-season grass | 600 to 1,000 |
*Response is based on effective water available (rainfall and/or irrigation) for plant growth. Soil water-holding capacity, growth conditions and application efficiency should be part of any irrigation planning program. |
Cool-season perennial grasses, such as tall fescue or orchardgrass, usually produce less response from irrigation than warm-season grasses, such as sudangrass or crabgrass. Growth responses to irrigation vary by soil type, species, plant stage of growth, season, total water available and time of harvest. Strategic use of nitrogen fertilizer can also optimize forage production as well.
University of Missouri forage irrigation research in 2017 and 2018 found that forage responses became more apparent when soil water availability was below 40 percent. Note that the forage growing conditions within those years were mostly adequate from a rainfall standpoint.
Types of forage irrigation systems
Missouri producers can irrigate forage using both low-pressure and high-pressure systems. This guide focuses on four typical systems: pod-line irrigation, low-pressure traveling irrigators, high-pressure traveling guns and center pivots.
Pod-line irrigation systems (low pressure)
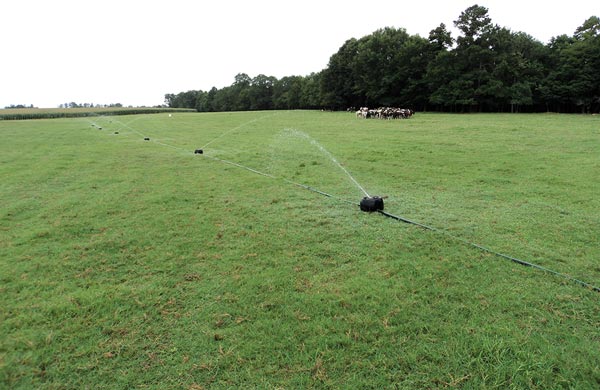
Pod-line irrigation systems are a series of sprinklers on a drag hose (Figure 3). The optimal pressure for the sprinkler system is typically 35 to 55 pounds per square inch (psi). Water requirements for this system vary by nozzle sizing and number of nozzles — typically about 3 gallons per nozzle per minute — but systems can be developed and sized according to the quantity of source water available. Each pod has the capacity to irrigate a 50-by-50 foot area. A typical 15-pod system can irrigate about 5 to 10 acres with one or two moves a day. The system can be moved by towing the entire line with an all-terrain vehicle (ATV), tractor or utility vehicle. Systems are typically moved once or twice daily, depending on how much water is applied, and passes are repeated on a seven- to 14-day rotation as needed.
The primary advantage of this system is its flexibility. It can be used on many field sizes and slopes. Systems can be customized (number of pods and nozzle types per system) to match the water source capabilities, and separate lines can be added to increase the acres covered. Pod-line systems have low capital investment costs and low maintenance requirements when compared to other systems.
Disadvantages of pod-line irrigation are that it must be moved manually once or twice a day and that it covers a limited area. Coverage can be scaled up with the purchase of additional pod-line systems, but each additional pod line increases daily labor needs. Further, some tall-growing crops are not suitable for pod-line systems because moving the lines mashes the forage.
Traveling irrigator (low pressure)
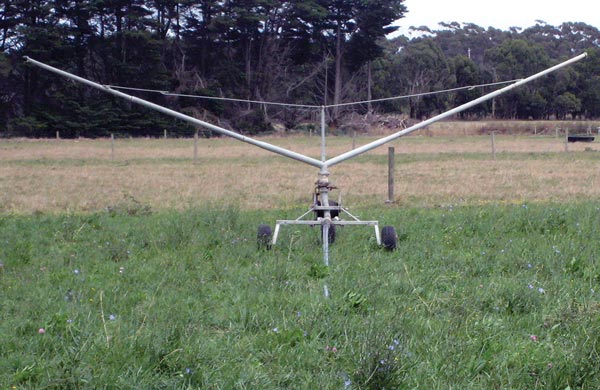
The low-pressure traveling irrigation system is a wheeled system used to spread effluent or to irrigate pasture (Figure 4). Nozzles spray water while constantly spinning in a circle. A cable attaches the irrigator to an anchored endpoint, along with a hose that supplies the water. The spinning causes a series of gears to move, reeling the irrigator in with the cable toward the endpoint. Optimal pressure needs for this sprinkler system will vary from 20 to 50 psi. A typical system will irrigate 20 to 40 acres.
Some benefits of a traveling irrigator include adjustable speeds, low cost, low pressure needs and ease of use in comparison to other irrigation systems. This system can effectively irrigate a variety of field sizes and shapes in straight lines.
A disadvantage is the daily labor requirement. The system must be reset for each path, and the travel distance is limited by the cable and hose length.
Traveling gun (high pressure)
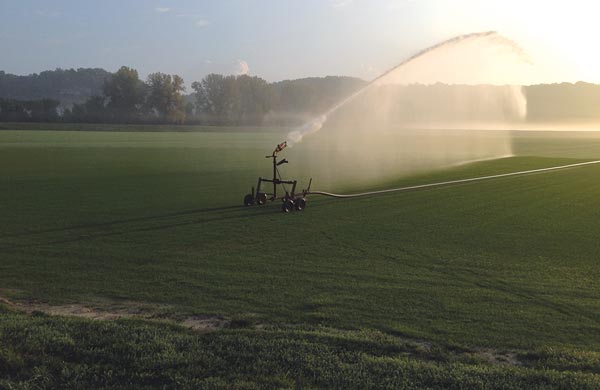
A high-pressure traveling gun irrigation system is made up of a large sprinkler gun on a wheeled cart and a reel system (Figure 5). Traveling guns require pressure ranging from 60 to 120 psi and with adequate pressure can irrigate a swath nearly 400 feet wide. The reel system is available in either a cable-tow (flexible hose) or hose-pull (hard hose) configuration. Cable-tow systems are anchored at the end of the field and are pulled by a winch on the cart, powered by an engine or a water drive. A hose-pull system works similarly, but uses the onboard hose reel to pull itself across the field. Most traveling guns can cover 80 to 100 acres per gun.
A major advantage of the traveling gun system is its flexibility. It can accommodate fields of many sizes and shapes. Additionally, it can put on more water and cover larger acreages than low-pressure traveling irrigator or pod-line systems.
Disadvantages of a traveling gun system are that operating costs and energy requirements tend to be high. Additionally, daily labor needs are high as the system requires a new setup after each path is completed.
Center pivot (low or high pressure)
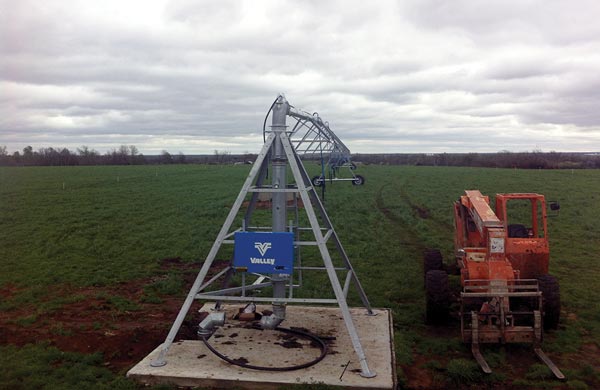
A center pivot is a self-propelled system with a series of sprinklers that rotates around a pivot point (Figure 6). Depending on how many acres are being irrigated, several towers are linked together to make up the system. Typically the length of the system is 10 towers, which would equal 1,320 feet, or a quarter mile. With each additional tower added, the number of acres irrigated and total travel distance increases at an accelerated rate. Center-pivot systems are available in towable or nontowable (fixed at the pivot point) units. Electric or hydraulic drive systems can be used to propel the center pivot. Sprinklers can be adjusted for low or high operating pressures.
The advantages of the center-pivot system contribute to its wide usage. The area irrigated by the system can be adjusted by changing the number of towers. Control systems can be sophisticated or simple and can even be operated remotely by wireless communications. These systems have comparatively low labor and maintenance requirements. In addition, pivot systems can be used to cool cows or to spread effluent by either using the same irrigation line or hanging additional lines on the system.
Disadvantages of a center-pivot system include not all fields are conducive to their use and total capital investments may be higher than other systems. Center-pivot use is limited on land with slopes greater than 10 percent or a field shape that limits the circular rotation. Because of the system’s circular rotation, corner areas do not receive irrigation unless you invest in a corner system. Also, retrofitting a center pivot into an existing grazing system with fencing and other existing infrastructure can be challenging. Additionally, capital investments for small pivot systems tend to be higher on a per acre basis than those for pod-line, traveling irrigator or traveling gun systems. However, center pivots become exponentially cheaper to install per irrigated acre when they span longer distances and can make a full rotation. This makes them more suitable for areas with large open fields.
Economics
The decision to invest in a forage irrigation system should be carefully analyzed from a financial standpoint. For beef and dairy producers, investing in additional forage inventories and storage for harvested forages may be cheaper than developing irrigation as a means of drought mitigation. Still, many farmers see irrigation as a better way to assure normal operations during rainfall shortages.
Generally, larger irrigation systems have lower irrigation investment per acre and lower operating costs per acre than smaller systems. For many farmers, the choice of irrigation system depends on the capacity of the water system, the time they are willing to spend irrigating, and the field size and shape.
When deciding whether to invest in a forage irrigation system, you should consider both ownership and operating costs.
Ownership costs
Capital investments include equipment, piping, pumps, storage and system installation. All assets decrease in value over time. Economic depreciation is a method of recognizing the annual cost of the one-time investment in those assets. Each investment has an expected useful life (in years) and an anticipated salvage value at the end of its useful life. Economic depreciation is calculated by subtracting the salvage value from the purchase price, and dividing the balance by the assumed years of useful life.
Interest is considered on a capital investment. Producers may purchase equipment with equity or use debt financing. Even if assets are purchased with equity, there is an opportunity cost of not using those funds on another alternative. One method for calculating interest costs is to multiply the average capital investment (purchase price plus salvage value, divided by two) by an annual interest rate.
Missouri collects personal property tax on farm equipment. The market value of equipment is multiplied by an assessment level — 12 percent for farm equipment — to arrive at an assessed value. The assessed value is then multiplied by the local tax rate, which varies by county or jurisdiction, to derive the property tax owed. Insurance premiums will vary by insurance carrier and policy chosen.
Operating costs
Operating costs for an irrigation system include power, labor, repair and maintenance. Irrigation power units require energy to pump water and pressurize the system. Power units may be electric motors or combustion engines. In general, electricity tends to have energy and labor efficiency advantages over liquid fuels. But in some cases, getting electricity to the location can be cost-prohibitive. Major factors that will affect the pumping cost include the price of fuel, operating pressure (psi), pumping lift (depth) and volume of water applied.
Labor is needed to setup and operate irrigation equipment. Producers should factor the cost of labor — including benefits and taxes — to perform irrigation duties. Repairs and maintenance are required to keep irrigation equipment and power units operational. The expected costs will vary by component (pump, engine, well, pipe, etc.), usage and age. Estimated annual maintenance costs for irrigation system and its components will typically range from 0.5 to 5 percent of average capital investment.
Economic examples of irrigation systems
The economics of various irrigation systems are presented in Tables 2, 3, 4 and 5. Assumptions and costs were generalized and can be customized to any farmer’s situation. To simplify the examples, they assume that you already have access to a lake, river or well that can provide the sufficient water quantity and rate, and that the forage response from irrigation is 600 pounds of dry matter per acre-inch water. Each of the examples includes a return on investment calculation, with a standard of $150/ton forage value. Table 6 summarizes these scenarios.
Table 2. Pod-line irrigation system (10 acres).
Type of cost/assumption | Annual cost ($) | Per acre ($) | |
---|---|---|---|
Depreciation | 15 years of useful life | 745.83 | 74.58 |
Interest | 8.50% of avg. investment | 499.59 | 49.96 |
Taxes | 0.25% of avg. investment | 14.69 | 1.47 |
Insurance | 0.50% of avg. investment | 29.39 | 2.94 |
Labor | 60 hours (6 hours per irrigation) |
1,200.00 | 120.00 |
Repair | 3% of avg. investment | 255.78 | 25.58 |
Power | Electric @ $0.13 per kilowatt hour, 3.4 hp | 452.98 | 45.38 |
Total annual costs | 3,198.26 | 319.83 | |
Irrigation cost per ton of dry matter | 71.07 per ton | ||
Return on investment | 57% |
Table 3. Traveling irrigator (low pressure) (30 acres).
Type of cost/assumption | Annual cost ($) | Per acre ($) | |
---|---|---|---|
Depreciation | 15 years of useful life | 1,413.33 | 47.11 |
Interest | 8.50% of avg. investment | 901.00 | 30.03 |
Taxes | 0.25% of avg. investment | 26.50 | 0.88 |
Insurance | 0.50% of avg. investment | 53.00 | 1.77 |
Labor | 90 hours (9 hours per irrigation) |
1,800.00 | 60.00 |
Repair | 3% of avg. investment | 318.00 | 10.60 |
Power | Electric @ $0.13 per kilowatt hour, 11.3 hp | 1,417.62 | 47.25 |
Total annual costs | 5,929.46 | 197.65 | |
Irrigation cost per ton of dry matter | 43.92 per ton | ||
Return on investment | 96% |
Table 4. Traveling gun (high pressure) (60 acres).
Type of cost/assumption | Annual cost ($) | Per acre ($) | |
---|---|---|---|
Depreciation | 15 years of useful life | 4,910.00 | 81.83 |
Interest | 8.50% of avg. investment | 3,130.13 | 52.17 |
Taxes | 0.25% of avg. investment | 92.06 | 1.53 |
Insurance | 0.50% of avg. investment | 184.13 | 3.07 |
Labor | 90 hours (9 hours per irrigation) |
1,800.00 | 30.00 |
Repair | 3% of avg. investment | 1,104.75 | 18.41 |
Power | Electric @ $0.13 per kilowatt hour, 44.5 hp | 5,965.20 | 99.42 |
Total annual costs | 17,186.26 | 286.44 | |
Irrigation cost per ton of dry matter | 63.65 per ton | ||
Return on investment | 55% |
Table 5. Center pivot (low pressure) (134 acres).
Type of cost/assumption (diesel) | Annual cost ($) | Per acre ($) | |
---|---|---|---|
Depreciation | 25 years of useful life | 7,821.84 | 58.30 |
Interest | 8.50% of avg. investment | 8,301.14 | 61.95 |
Taxes | 0.25% of avg. investment | 244.15 | 1.82 |
Insurance | 0.50% of avg. investment | 488.30 | 3.64 |
Labor | 20 hours (2 hours per irrigation) | 400.00 | 2.99 |
Repair | 3% of avg. investment | 3,115.21 | 23.25 |
Power (Diesel) | Diesel @ $4.05 per gallon, 224 hp | 45,396.90 | 338.78 |
Total annual costs | 65,758.55 | 490.74 | |
Irrigation cost per ton of dry matter | 109.05 per ton | ||
Return on investment | 46% |
Assumptions for electric power that vary from diesel | |||
---|---|---|---|
Labor | 10 hours (1 hour per irrigation) | 200.00 | 1.49 |
Repair | 3% of avg. investment | 2,184.32 | 16.30 |
Power (Electric) | Electric @ $0.13 per kilowatt hour, 185.8 hp | 20,872.32 | 155.76 |
Total annual costs | 36,872.45 | 275.17 | |
Irrigation cost per ton of dry matter | 61.15 per ton | ||
Return on investment | 53% |
Table 6. Comparison of various irrigation systems and scenarios.
Input | Pod-line | Travelling irrigator | Travelling gun | Center pivot (diesel) | Center pivot (electric) |
---|---|---|---|---|---|
Area covered (acres) | 10 | 30 | 60 | 134 | 134 |
Irrigations | 10 | 10 | 10 | 10 | 10 |
Inches per irrigation | 1.5 | 1.5 | 1.5 | 1.5 | 1.5 |
Total volume applied (million gallons) | 4.1 | 12.2 | 24.4 | 54.6 | 54.6 |
Operating pressure (psi) | 37 | 40 | 120 | 40 | 40 |
Water source | Surface | Surface | Surface | Deep well | Deep well |
Total horsepower needed | 3.4 | 11.3 | 44.5 | 224 | 186 |
Total capital investment ($) | 11,755 | 21,200 | 73,650 | 195,321 | 172,021 |
Additional forage produced (tons of dry matter) | 45 | 135 | 270 | 603 | 603 |
Annual operating cost ($) | 1,909 | 3,536 | 8,870 | 48,912 | 23,257 |
Cost per dry matter ton gained from irrigation ($) | 71.07 | 43.92 | 63.65 | 109.05 | 61.15 |
Decision support tool
The Forage Irrigation System Cost Analyzer (XLSX) is a spreadsheet tool that helps producers estimate the cost of using forage irrigation. You can use it to develop an irrigation system based on time and water needs, estimate an irrigated forage response, and detail irrigation costs to get an economic summary of a system. Additionally, it can help plan pipe and pump sizing for your situation.
For more information
For more information about irrigation systems, contact a local irrigation company or dealer. They can help customize irrigation systems around your farming situation and provide irrigation technical assistance and specific cost information.
Sources
- Henggeler, J.C. 1988. Irrigation systems for forage crops. Guide B-1611. Texas Agricultural Extension Service.
- Henggeler, J.C. 2012. Irrigation systems, wells, and pumps of the Mississippi River Alluvium Aquifer of Southeast Missouri. Columbia: University of Missouri Extension.
- Hoffman, T. R. and G. S. Willet. 1998. The economics of alternative irrigation systems in the Kittitas Valley of Washington state. Farm Business Management Reports EB1875. Washington State University Cooperative Extension.
- Scherer, Thomas, et al. 1999. Sprinkler irrigation systems. Ames, IA: MidWest Plan Service.
- Scherer, Thomas. 2018. Selecting a sprinkler irrigation system. AE-91 Guide. North Dakota State University Extension Service.
- Volesky, J. D. and A. L. Berger. 2010. Forage production with limited irrigation. Neb Guide G2012. Lincoln: University of Nebraska-Lincoln Extension.
This material is based upon work supported by the USDA/NIFA under Award Number 2012-49200-20032.
Original authors
Ryan Milhollin, Ray Massey, Joe Horner, Joseph Zulovich and Rob Kallenbach