Aflatoxin is a term generally used to refer to a group of extremely toxic chemicals produced by two molds, Aspergillus flavus and A. parasiticus. The toxins can be produced when these molds, or fungi, attack and grow on certain plants and plant products. In the United States, aflatoxin production occurs when A. flavus and A.parasiticus attack peanuts, cottonseed, white and yellow corn, certain nuts and wheat. Most of the aflatoxin problems on corn in the United States are caused by A. flavus, and the most potent toxin produced by this mold is called aflatoxin B1. Drought, extreme heat and corn ear injury from insect feeding stress the corn and create an environment favorable to these molds and to aflatoxin production.
Aflatoxins pose a low-level threat to U.S. food safety because regulations and testing by federal agencies and industry exclude contaminated products from the food supply. Generally, these programs have been successful in protecting U.S. consumers from aflatoxin-contaminated food. The Food and Drug Administration (FDA) has established guidelines for aflatoxins in corn used for food and feed in the United States (Table 1).
Problems with aflatoxin-contaminated corn have been most severe and occurred most often in the southern and midsouth regions of the United States. In Missouri severe problems with aflatoxin-contaminated corn developed in 1971, 1975, 1980, 1983, 1988, 1993, and 1998 and were most severe in 1993 and 1998. The loss in income for Missouri corn farmers due to aflatoxin contamination was estimated at $10 million in 1993 and $20 million in 1998.
Table 1. Maximum acceptable levels of aflatoxins in corn used for food and feed, as established by the Food and Drug Administration (parts per billion).
Corn commodity | Maximum acceptable level of aflatoxins |
---|---|
Products intended for food use by humans | 20 ppb |
Feed for dairy animals or immature animals (including immature poultry) | 20 ppb |
Feed for which the intended use is not known | 20 ppb |
Feed for breeding beef cattle, breeding swine or mature poultry (e.g., laying hens) | 100 ppb |
Feed for finishing swine (i.e., 100 lb. or more) | 200 ppb |
Feed for finishing beef cattle (i.e., feedlot cattle) | 300 ppb |
Growth of Aspergillus flavus
The fungi A. flavus and A. parasiticus are widely distributed in nature, although A. flavus is more common in Missouri. A. flavus has been reported to occur on many types of organic material, including forages, cereal grains, food and feed products and decaying vegetation in cultivated soils. A. flavus can also produce specialized survival structures that enable the fungus to survive in the soil for extended periods.
In the field
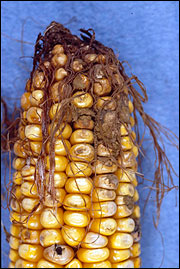
Initially it was believed that growth of A. flavus occurs on corn only in storage. But it has since been shown that A. flavus can also attack corn in the field. Field infection of corn by A. flavus can result in aflatoxin production in the corn before harvest. The fungus is able to invade through the corn silks or in association with insect damage to kernels and ears.
Temperatures ranging from 80 to 100 degrees F and a relative humidity of 85 percent are optimum for A. flavus growth and aflatoxin production. Periods of drought and heat stress during the growing season, especially during pollination and as kernels mature, favor A. flavus infection. Corn damaged by insects or weather conditions such as hail, early frost that cracks the kernels, and wind storms may also be predisposed to infection by A. flavus.
On corn in the field, A. flavus is evident as a greenish yellow to yellowish brown, feltlike or powdery mold growth on or between the corn kernels. Mold growth is more likely to develop adjacent to or in insect-damaged kernels on ears (Figure 1).
In storage
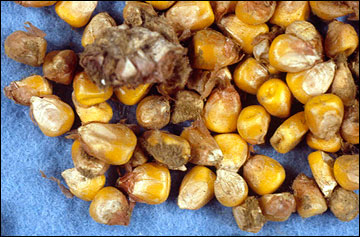
A. flavus can also develop or continue to develop on corn in storage (Figure 2). The extent and severity of both invasion by A. flavus and production of aflatoxins in stored corn are influenced by various grain and storage conditions such as moisture content and temperature of the stored grain, physical condition of the grain going into storage, and length of storage.
A. flavus grows best on corn at 18.0 to 18.5 percent moisture. Moisture content below 13 percent prevents growth of A. flavus. Fungal growth may begin on corn at a moisture content lower than 18 percent. Then as the fungus grows, respiration occurs, releasing heat and moisture into the surrounding environment in the grain mass. This results in an increase in the moisture content and temperature of the surrounding corn, causing a hot spot. If moisture content and temperature continue to rise, the environment for A. flavus becomes more favorable.
A. flavus grows best at high temperatures. The fungus will grow slowly in grain between 40 and 50 degrees F but will grow rapidly in grain at 80 to 90 degrees.
Corn contaminated with A. flavus going into storage will deteriorate at lower moisture content, at a lower temperature and in a shorter time than grain that is free or almost free of A. flavus. Corn with cracks or breaks in the seed coats, broken kernels or other physical damage is more subject to invasion by A. flavus.
It is important to note that the presence of A. flavus on corn does not necessarily mean that aflatoxins are also present in that corn. Circumstances that favor mold growth may also favor mycotoxin production, but mold growth can also occur with little or no mycotoxin production.
Aflatoxin production
There are several different toxins in the aflatoxin group. They are designated aflatoxin B1 and aflatoxin B2 (because they appear blue under ultraviolet, or UV, light), aflatoxin G1 and G2 (because they appear green under UV light) and aflatoxin M1, which may be found in milk of cows fed aflatoxin-contaminated feed.
Although it has been known for more than 100 years that some kinds of moldy grains when eaten by animals or humans could cause illness, intensive study of mycotoxins and the illnesses caused by mycotoxins only dates from the 1960s. In 1960 scientists determined that the deaths of more than 100,000 turkey poults in England were due to a toxic substance in the peanut meal ration fed to the birds. The toxin was a product of the mold A. flavus growing in the meal. The toxin was soon purified, chemically characterized and named aflatoxin. The word “aflatoxin” was formed by adding the “A” from the genus name Aspergillus and “fla” from the species name flavus to the word “toxin.” Feeding tests with laboratory animals showed that aflatoxin in amounts of a few parts of toxin per billion (ppb) parts of feed could cause serious injury, including fatal liver cancer, to animals.
Aflatoxins are extremely durable under most conditions of storage, handling and processing of seeds or in foods or feeds made from contaminated seeds. Aflatoxins are highly stable when exposed to heat and will withstand boiling in water. Toxin levels in corn may decline in storage but still be present after seven years.
Aflatoxins become more prevalent and therefore more of a food safety concern during a drought because low rainfall and high temperatures encourage the growth and survival of the molds that produce the toxins. Also, crops stressed by drought and high temperatures or weakened by insect or other damage (such as hail or frost) are more susceptible to mold growth and subsequent aflatoxin contamination. There are methods for preventing or minimizing the production of aflatoxins on field-grown corn and on corn in storage (see text box).
Sampling and testing for aflatoxins
Typically, aflatoxins are not distributed uniformly through a field of corn or mass of grain. Improper sampling of the field or grain mass can result in misleading (either high or low) mycotoxin levels when samples are analyzed for aflatoxin concentration. It is extremely important to collect samples that are representative of the entire grain mass. A good composite sample consists of subsamples taken from every part of a load, bin or unit of corn.
Field sampling is difficult. If a corn combine is used, make one or more passes the entire length of the field. As the hopper is being emptied, pass a cup through the moving stream at 30-second intervals until the collected volume totals 10 pounds. Mix this well and save for testing.
Sampling from loads of grain or stored grain must be done carefully to ensure that a representative sample is taken. The recommended procedure is to sample during loading or transfer of grain by passing a cup through a moving stream of grain at frequent intervals (for example, every minute) and combining the samples for a representative, composite sample. Probe sampling is acceptable if grain is not being moved or transferred. Again, it is important to take a number of probes and combine these into one representative sample. The initial sample should be about 10 pounds. This sample should be mixed thoroughly before a subsample is tested.
The final step in the analysis for aflatoxins is to determine whether they are present in a sample and, if so, in what concentration. There are several methods of checking corn for the presence of aflatoxins. Various rapid test kits may be used in the field, on the farm or at the elevator to detect the presence of aflatoxins and, in some cases, quantify the level present. Laboratory tests such as the minicolumn, thin layer chromatography and gas chromatography can give quantitative results. The so-called black light screening method for aflatoxins in corn is based on a characteristic bright greenish yellow fluorescence (BGYF) visible on the corn kernels when examined in a darkened room under long-wave ultraviolet light, a black light. This fluorescence is the result of properties of kojic acid, a compound produced by A. flavus but not related directly to aflatoxins. This technique is not specific for aflatoxins and is not reliable. Other methods should be used to detect aflatoxins.
Rapid test kits (ELISA kits)
Several commercial firms have marketed rapid test kits based on enzyme-linked immunosorbent assays for use in determining the presence of aflatoxins in corn samples. These test kits are self-contained and provide all necessary instructions to complete analysis on the farm, at the elevator or at the buying point. Several kits are available from Seedburo Equipment Company in Des Plaines, Illinois, and Neogen Corporation in Lansing, Michigan, at prices ranging from $8 to $15 per sample). However, some additional equipment is needed to process the samples.
Minicolumn test
The minicolumn test is a more determinative test for aflatoxins. It is quick, relatively inexpensive and can be performed at the buying point. A concentrated corn extract is passed through a minicolumn tube that contains layers of alumina and silica gel. After treatment with a developing solution, a fluorescent blue band appears. The color intensity of the blue fluorescence is directly proportional to the aflatoxin level, but in most cases the minicolumn test is used only to identify lots with concentrations in excess of 20 ppb. If the sample used for analysis is representative of the entire load, it is an acceptable method for determining whether to accept or reject loads.
Thin layer chromatography
Thin layer chromatography is a more precise measure of aflatoxin concentrations in corn. This method, often used by testing laboratories, involves extraction with chloroform followed by purification on a silica gel column for quantitative thin layer chromatography. If this method is coupled with extraction methods approved by the Association of Official Analytical Chemists, it is superior to other methods of quantifying aflatoxins.
Testing laboratories
Samples for aflatoxin testing can be submitted to the Veterinary Medical Diagnostic Laboratory, College of Veterinary Medicine, P.O. Box 6023, Columbia, MO 65205 (phone: 573-882-6811). The sample should consist of a half pound of grain that is representative of the entire load or volume of grain. There is a $41.00 fee for aflatoxin analysis as of January 2010.
Reducing aflatoxins in corn and feed
Many methods for lowering the aflatoxin levels in corn have been tested, but most are not effective or are only partially effective.
Mechanical separation
Screening removes broken kernels, which often contain a high percentage of the aflatoxin contamination. Screening coupled with the use of gravity separation machines removes most lightweight, infected kernels and thus further reduces the aflatoxin concentration in food-grade corn. The method is legal and can be somewhat effective. It is important to remember that the screenings will contain a high level of aflatoxin-contaminated material and should be used with care.
Blending
The mixing of contaminated (greater than 20 ppb) corn with uncontaminated (less than 20 ppb) corn is not usually a recommended practice. Blending corn lots to reduce the level of aflatoxins in corn going into interstate trade is prohibited by the FDA. In 1998 special permission was obtained to allow the adulteration of uncontaminated corn in Missouri by “blending” with corn containing aflatoxins. This permission has expired.
Detoxifying
Aflatoxins are heat stable and are not completely destroyed by boiling the grain in water or roasting. Microwave treatment of corn meal reduces aflatoxin B1 and B2 levels, but this method is expensive and toxin destruction is not complete. Currently, there is no FDA-approved or sanctioned method for “detoxifying” — through ammoniation or other means — corn that contains aflatoxins. As of 2003, Texas, North Carolina, Georgia and Alabama have implemented state policies that allow ammoniation of corn as well as cottonseed. Corn ammoniated under these specific state policies is prohibited from being distributed in interstate commerce and is subject to labeling and feeding restrictions. This policy is not approved in Missouri.
Additives to feed
Research has shown that the addition of certain dietary additives may reduce the absorption of aflatoxins by the gut of some animals. These dietary additives include various clay minerals such as bentonites and hydrated sodium calcium aluminosilicates (HSCA). At a concentration of 0.5 percent of the diet, the aluminosilicates are very effective at binding aflatoxins and preventing their absorption in both ruminants and nonruminants. These dietary additives are legally sold as anticaking agents, but their use in detoxifying mycotoxins has not been approved by the FDA.
Alternative uses for contaminated corn
Corn with an aflatoxin content of 20 ppb or more may not be sold for interstate commerce. Aflatoxin-contaminated corn may be used locally for animal feed only if the FDA guidelines are met (Table 1). Acceptable methods for disposing of corn that cannot be fed are limited. The corn may be spread on fields and tilled into the soil and it may be used for making ethanol. The aflatoxins are not destroyed by fermentation and will be concentrated in the dry distillers grain. Ethanol or gasohol facilities may screen incoming loads for aflatoxins and reject contaminated loads because of concerns about aflatoxin levels in byproducts that may be used for feed.