Hardwood lumber may be dried for many reasons. First, drying increases dimensional stability. Wood shrinks considerably more across the grain than along the grain when it dries. Because wood shrinks during drying, if it is cut to size before properly dried, it will be undersized in its final form. Second, drying can reduce, or even eliminate, decay or stain. Wood dried below 20 percent moisture content is not susceptible to decay or sap staining. Third, drying reduces weight. Removal of most of the water in the wood reduces lumber weight by 35 percent or more. Finally, drying increases the stiffness, hardness and strength of wood. Most species of wood increase their strength characteristics by at least 50 percent during the process of drying to 15 percent moisture content.
Air-drying and solar kiln drying are the most economical ways to remove much of the water from green lumber. Correct exposure of lumber to the outside air can reduce moisture content to 14–19 percent; lumber at this moisture content is suitable for many construction uses and exterior applications. Solar kiln drying can reduce the moisture content of lumber to 7–8 percent so it can be used in furniture and other applications within a heated building. Further drying beyond air and solar drying is usually accomplished in a dry kiln where temperature, humidity and air circulation can be carefully controlled.
Proper stacking of lumber
Lumber is stacked in a special way to maximize the surface of each piece of lumber exposed to the air and to support each piece so it will dry straight and without unnecessary warping. Proper stacking of lumber for air-drying involves building a strong foundation, careful placing and spacing of the boards in the stack, and providing roof protection (Figure 1).
Locate the lumber stack on a level site with good drainage and exposure to prevailing winds. Orient the stack so that the prevailing winds blow across the boards. Covering the ground beneath and around the stack with black polyethylene can help prevent moisture from moving from the soil to the wood, and weeds and grass from growing and restricting air movement.
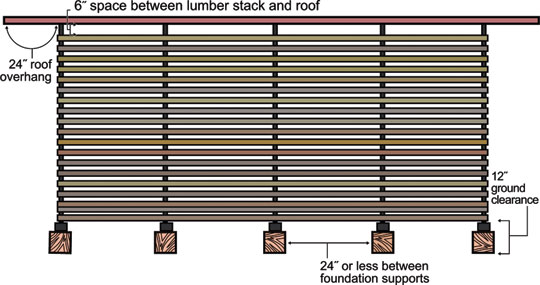
Foundation
Start with a good foundation. Various materials such as railroad crossties, treated wood beams or concrete blocks can be used to build the foundation and support the stack. The supports should be tall enough so the first layer of boards to be dried is at least 12 inches above the ground. They should be spaced no more than 24 inches apart to provide adequate support for the lumber stack. The cross-supports should be aligned because any low or high spot or twist from opposite corners of the stack will result in lumber with the same amount of warp.
Stack
Ideally, the lumber should be sorted by length and thickness. Lumber of the same length should be put in one stack. If this is not possible, you can “box pile” the lumber (Figure 2): For each layer, place the long boards on the edges of the stack. These outside boards help tie the stack together, making it less subject to tilting or falling over. Place shorter boards on the inside, flush with alternating ends of the stack. Do not let loose ends overhang without support.
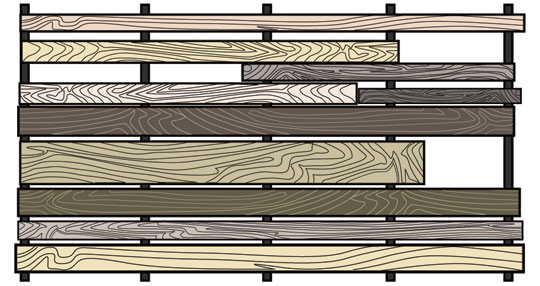
Do not mix lumber of varying thickness within the same layer. Put thicker lumber on the bottom of the stack. This positioning prevents some handling of the heavier stock, and the weight from the top of the stack will restrain the thicker material as it dries, preventing excessive warping. Furthermore, the thick stock will take longer to dry. If you plan to use certain boards first, place them near the top of the stack for easier access.
Stack the lumber in neat layers as soon after sawing as possible. Leave a 1- or 2-inch space between boards within a layer. Wood strips, called “stickers,” provide the space between layers to allow air movement. Place stickers perpendicular to the length of the lumber and directly over the foundation crossbeams to space each layer. Stickers should be straight, uniformly thick, free of bark decay and stain, and thoroughly dry. Stickers are commonly 1 inch thick by 11/2 inches wide. The length of the stickers should be the width of the lumber stack. Building lathe doubled in thickness can be used if nothing else is available.
The stack should be only as high as you can comfortably and safely stack the boards; usually no more than head-high. If properly stacked, the weight of the lumber helps prevent excessive warping in all but the top layers. Therefore, low-grade boards should be placed on the top of the stack. Weights such as concrete blocks can be used to restrain the top layers.
Roof
The lumber stack should be covered. Practically any device that sheds water can be used as a roof. The roof should extend 24 inches beyond the front, back and each side of the stack. Leave an air space of 6 inches between the top of the stack and the roof.
Minimizing degrade during drying
Stresses develop in lumber as moisture is lost during drying. Shrinkage in width and thickness will occur; warp, checks or other defects may develop. The potential for drying defects such as checking and warping also increases with greater lumber thickness.
Warping can be minimized through proper stacking technique and adding weight to the top of the stack (about 40 pounds per square foot).
Lumber dries several times faster from the ends of a board than from the surface or edges. As a result, wide boards often crack severely. This defect is called “checking.” Checking can be reduced by coating the ends of the boards with a commercial wax emulsion sealer, such as Anchorseal, or aluminum paint in a spar varnish base. However, end-coating the lumber will slow drying rates and is only appropriate for higher-quality lumber.
Drying time
The rate at which properly stacked green lumber dries depends on the wood characteristics, the lumber thickness and the climatic conditions.
Heavier hardwoods require longer drying times than lighter woods. Some species of wood have higher green moisture content than others; sapwood and heartwood may have quite different drying characteristics.
Drying time required increases rapidly with increase in lumber thickness. For example, 2-inch thick lumber may take from two to four times longer than 1-inch lumber. Do not saw lumber any thicker than is necessary for the intended use (after allowing for shrinkage and surfacing) if drying speed is important.
The climate and the season in which green lumber is exposed have a major influence on the time required to air-dry lumber. Temperature perhaps is the most influential factor, but rainfall and humidity are also important. Green lumber stacked during the warm months will typically dry much faster than lumber exposed during the late fall and winter.
The U.S. Department of Agriculture (USDA) Forest Products Laboratory has estimated the air-drying times for several hardwood species at selected locations across the United States (http://www.fpl.fs.fed.us/documnts/fplgtr/fplgtr121.pdf - no longer available online. See search results.); the graphs in Figure 3 are for 4/4 (1-inch thick) and 8/4 (2-inch thick) boards of northern red oak drying in Columbia, Missouri.
Figure 3 clearly shows the effect on drying times of time of year when the lumber is stacked and board thickness.
Lumber at 15–20 percent moisture content is adequate for building unheated structures such as garages or barns. If the wood is to be used inside a heated structure, further drying in a commercial kiln to reduce moisture content to 6–8 percent is required.
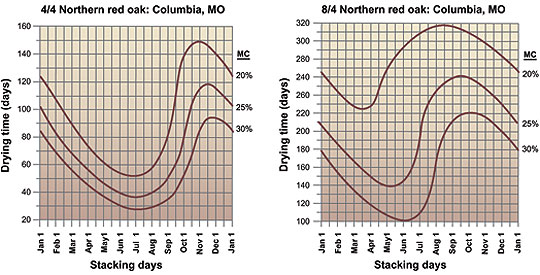
Problem
If 4/4 northern red oak is stacked on Aug. 1, how many days are required for the moisture content to reach 20 percent?
Solution
Locate Aug. 1 on the horizontal axis of the 4/4 graph and go up to the 20 percent moisture content (MC) curve. Notice that the 20 percent MC curve intersects the Aug. 1 vertical grid line at 60 days. Thus, the air-drying time to 20 percent MC for 4/4 northern red oak stacked on Aug. 1 is estimated to be 60 days. Note that 8/4 lumber stacked on Aug. 1 will require almost 320 days to reduce MC to 20 percent.
Figure 3. Example wood drying-time graphs. (Source: Simpson, W.T., and C.A. Hart. 2000. Estimates of air drying times for several hardwoods and softwoods. Gen. Tech. Rep. FPL–GTR–121. Madison, WI: U.S. Department of Agriculture, Forest Service, Forest Products Laboratory.)
Original author: James Pastoret